A comparison of LCD laminating and defoaming machines' primary requirements and capabilities
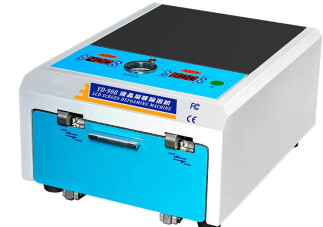
Introduction
An essential piece of equipment in the production process of liquid crystal displays (LCDs) is the LCD laminating defoamer, whose performance has a direct impact on the finished product's clarity and dependability. The lamination and defoaming process is a crucial stage in determining the product's quality. In order to assist the relevant businesses in making better selections, we will evaluate the features of the popular models on the market and go over the primary factors for choosing a laminating and defoaming machine.
I. Choosing the primary standards for LCD laminating defoamers
The following primary factors should be taken into account when selecting an appropriate LCD laminating and defoaming machine:
1. System for controlling temperature: For effective bubble removal, the OCA adhesive must reach its ideal fluidity within the proper temperature range, which is ensured by precise temperature control. A steady temperature environment also contributes to better product consistency and quality.
2. Pressure system: While a moderate pressure profile can prevent screen damage or adhesive overflow brought on by excessive pressure, high pressure can effectively encourage the fusing of bubbles and OCA adhesive. As a result, selecting equipment with real-time pressure monitoring and adjustable pressure output is essential.
3. Time Setting: The duration of the holding period must be freely modified in accordance with various production needs. While too long a time may reduce manufacturing efficiency, too short a time could not be able to totally eradicate air bubbles. In order to satisfy a variety of production demands, it is essential to select a machine with a customisable time setting feature.
4. Safety Performance: Safety precautions need to be taken because of the equipment's high temperature and high pressure operating environment. This covers safety precautions during operation, overheating protection, and overpressure protection. Furthermore, one of the necessary safety measures to guarantee that the machine can be promptly stopped in the case of an emergency is an emergency stop button.
5. Operational simplicity: Intelligent user interfaces that support touch screen operation and PLC programming control are typically found in modern laminating and defoaming machines, simplifying and facilitating the execution of intricate procedures. It's also important to take into account the equipment's maintenance costs and how simple it is to swap out worn parts.
6. Brand reputation and after-sales service: Selecting a well-known brand entails a better after-sales service system in addition to more dependable product quality. Timely and efficient technical support may minimise downtime and guarantee production continuity in the case of technical issues or the need for repair.
Comparing the Functions of the Mainstream Model
1. The Youshuo ELT high-pressure defoaming machine has an adjustable pressure setting and an intelligent temperature control mechanism, making it suited for LCDs of all sizes and types. It is particularly adept at managing huge LCD screens due to its highly effective defoaming capability.
Benefits include excellent user reputation, broad applicability, and high defoaming efficiency.
Cons: more expensive; might not be suitable for SMEs with tight budgets.
2. Features of the Zoyo ZY-QP Series De-foaming Machine: Offers a variety of model choices to satisfy various requirements. Operators with varying levels of expertise can choose between manual and automatic modes. designed to be small in order to conserve production space.
Benefits include a small footprint, flexible operation, and cost effectiveness.
One drawback is that manual models are not as efficient as fully automatic ones.
3. Tianxingjian AM-300 Laminating Machine: This fully automated device combines cooling, heating, and pressurisation into a single unit, making it appropriate for big production lines. The setup is customisable and can be changed to meet the demands of the user.
Benefits include process simplification, increased efficiency, and great customisability through integrated design.
The high technical requirements for operators and the substantial initial expenditure are drawbacks.
In conclusion
In conclusion, selecting the best LCD laminating defoamer necessitates careful evaluation of several aspects, including as ease of use, safety and security features, pressure range, and temperature control accuracy. In addition, it is crucial to select the best equipment model based on the particular requirements of the real production process. You will find the perfect option to satisfy your demands, whether you are searching for the best possible performance or cost-effectiveness. The laminating defoamer of the future will be more automated and intelligent as technology advances, giving consumers a better overall experience.