Why Specialized Hot Air Nozzles Are a Must for PCB Repairs
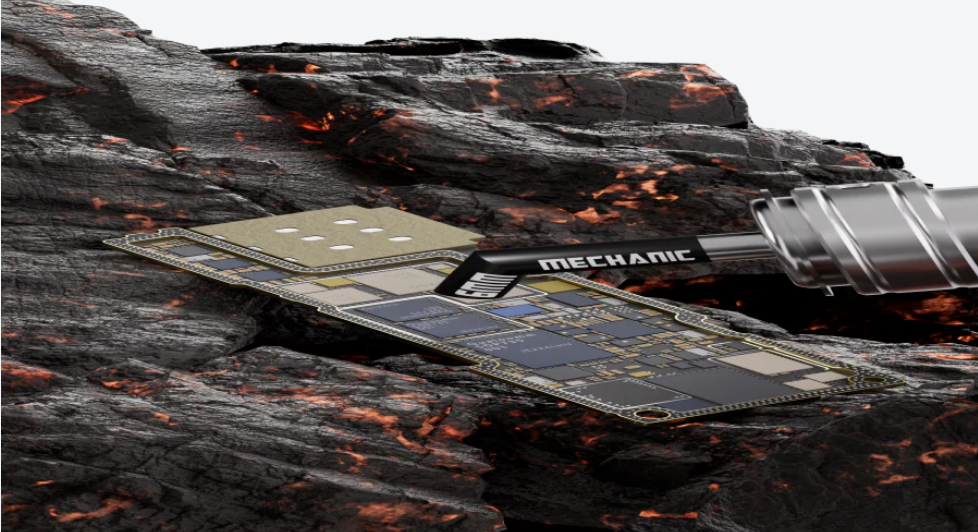
The importance of thermal management in circuit board repair cannot be ignored. Excessive heat or misdirection can lead to component failure or even damage to the entire board. To ensure a safe and efficient repair process, specialised hot air nozzles have become an indispensable tool for maintenance personnel. These tools provide precise control of temperature and airflow, reducing the risk of thermal damage and improving the quality of repairs. Next, we will discuss the application of professional hot air nozzles in PCB repair.
Firstly, the design of the hot air nozzle is critical, with the aim of concentrating and directing the airflow from the hot air rework station to ensure precise heating of a specific area without affecting surrounding components. Nozzle designs include 45° inclined nozzles, curved arc nozzles, etc. to suit different repair needs. In addition, high-quality nozzles ensure even airflow and prevent the creation of hot spots, thereby protecting the integrity of the entire board.
Secondly, choosing the right hot air nozzle is the key to ensuring the effectiveness of the repair. According to the specific needs of the repair task, such as small solder joints or FPC repair, BGA rework, etc., should choose the appropriate shape and size of the nozzle. For example, use a narrow and pointed nozzle or 45 ° angle design to focus the heat, while the choice of a wide round nozzle can ensure that the entire component is evenly heated. The material factor should not be overlooked either, as choosing heat-resistant steel nozzles will prevent air leaks and provide durability. In addition, the nozzle must be securely mounted on the hot air gun or BGA rework station to ensure optimum performance.
Further, there are a number of techniques that need to be mastered when using hot air nozzles. Correct temperature settings and airflow control are fundamental. Adjust the hot air station to the recommended setting for the component being repaired to avoid displacing small components. At the same time, maintaining the proper distance and angle, as well as a steady hand movement, are important factors in ensuring even heat distribution and minimising damage to the board. Regular cleaning of the nozzle to remove solder residue and oxidised build-up is also a key measure to maintain a stable airflow and prevent clogging.
Finally, professional hot air nozzles provide an efficient and safe tool for PCB repair, significantly reducing the risk of thermal damage through precise temperature control and airflow management. Choosing the right nozzle and using it correctly can improve the quality of repairs and ensure the long-term reliability of the board. However, attention to detail and operating practices are still required to ensure optimal repair results and equipment longevity.
In conclusion, professional hot air nozzles play a vital role in PCB repair. Through the rational selection and use of these tools, technicians can effectively control heat distribution and prevent thermal damage, thereby improving repair quality and efficiency. Therefore, both experienced engineers and novices entering the industry should be fully aware of the functions, applicability and proper use of hot air nozzles in order to maximise their potential in complex PCB repair tasks.