Automatic soldering machine use tips
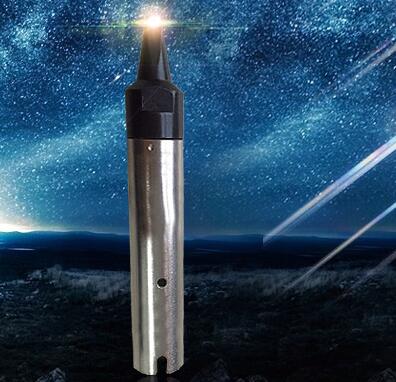
Automatic soldering machines are far ahead of hand soldering in terms of efficiency and precision, and even a skilled soldering tin can not perform soldering work consistently for long periods of time with high precision and high strength. However, when using automatic soldering machines, it is also necessary to master some basic techniques and methods that will allow you to become familiar with automatic soldering machines faster and to produce the perfect product.
1, the correct position of the tip correction:
In the use of automatic soldering machine welding process, the operator often in order to solder more precise position of the tip is very low, trying to use the tip of the welding force point. This is actually wrong, solder machine solder is heated by the contact area of heat, not through the head to heat Luo. Luo iron head of the welding force will cause weldment damage, as a serious product scrapped.
2, to maintain the right temperature:
If in order to shorten the heating time using high-temperature soldering iron soldering point, there will be another problem: the solder wire solder flux does not have enough time to diffuse the flow of premature volatilization failure; solder melting too fast Affect the role of flux play; as the temperature is too high, although the heating time is also caused by overheating. Conclusion: Keep the tip in a reasonable temperature range. The general experience is that the temperature of the soldering tip is 50 ° C higher than the melting temperature of the solder. The ideal state is to shorten the heating time at a lower temperature, although this is contradictory, but in practice we can get a satisfactory solution by operating practices.
3, master the heating time
Automatic soldering machine can be directly set in the control panel preheat time: soldering can use different heating rates, such as poor shape soldering iron head, with a small iron soldering large welding we have to extend the time to meet the temperature of the tin Claim. Prolonging the heating time in most cases is detrimental to the assembly of electronic products because the bonding layer of the solder joint exceeds the proper thickness for a long time to cause the solder joint performance to deteriorate. Material wetting weldment under the premise of the shorter the better.